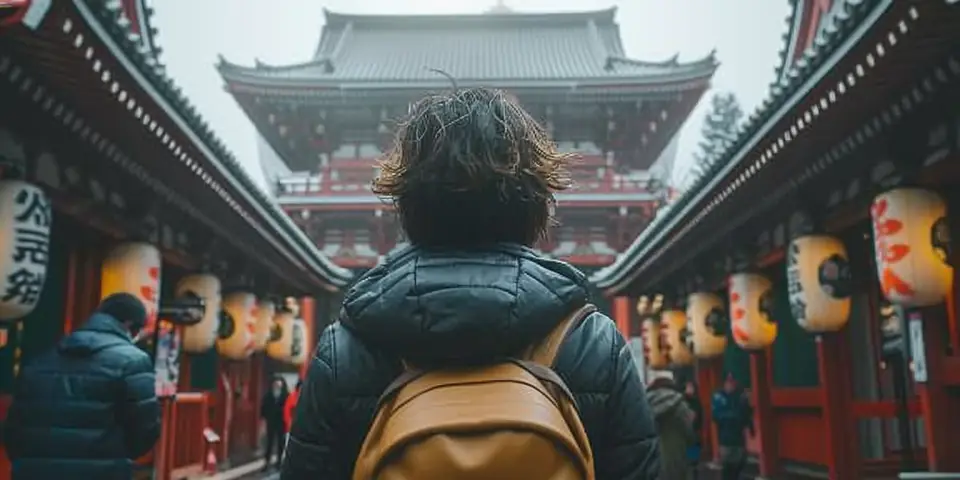
The 7-Minute Miracle: How Japan's Railway Industry Achieves Exceptional Cleaning Efficiency
Innovative Cleaning Strategies in Japan’s Railway Industry
Innovative Cleaning Strategies in Japan’s Railway Industry
Japan’s railway industry is renowned for its exceptional cleanliness and efficiency, with the famous “7-minute miracle” being a testament to this reputation. The country’s train cleaning crews have perfected the art of quickly and thoroughly cleaning trains, ensuring a comfortable and hygienic environment for passengers. So, what makes Japan’s railway industry stand out in terms of cleaning strategies?
One key factor is the emphasis on employee satisfaction and pride. Cleaning staff are trained to take ownership of their work, and their dedication to providing excellent service is evident in every aspect of the cleaning process. This focus on human capital has led to increased efficiency, as motivated employees strive to improve their performance and contribute to a positive passenger experience.
Another crucial element is the meticulous attention to detail exhibited by Japanese train cleaners. Every step of the cleaning process is carefully planned and executed, ensuring that no area is overlooked. This commitment to thoroughness is reflected in the sparkling cleanliness of Japan’s trains, which are a hallmark of the country’s railway industry.
To replicate this success, industries can learn from Japan’s approach by prioritizing employee engagement and empowerment. By fostering a sense of pride and ownership among staff, organizations can unlock increased productivity and efficiency. Additionally, adopting a meticulous approach to cleaning, where every detail is carefully considered, can lead to significant improvements in overall cleanliness and customer satisfaction.
In practical terms, this means investing time and resources into training and motivating cleaning staff, as well as implementing efficient processes that minimize waste and maximize productivity. By doing so, industries can reap the benefits of improved cleanliness, increased customer satisfaction, and enhanced reputation – all of which are essential for long-term success.
The Impact of Kaizen on Organizational Behavior and Leadership
The Impact of Kaizen on Organizational Behavior, Leadership, and Work Culture
The success of Japan’s railway industry in achieving exceptional cleanliness and efficiency is largely attributed to the adoption of kaizen, a philosophy that emphasizes continuous improvement and innovation. This mindset has permeated various aspects of organizational behavior, leadership, and work culture, leading to significant improvements in productivity, customer satisfaction, and employee motivation.
One key takeaway from Japan’s railway industry is the importance of prioritizing employee engagement and empowerment. By fostering a sense of pride and ownership among staff, organizations can unlock increased productivity and efficiency. This can be achieved by investing time and resources into training and motivating cleaning staff, as well as implementing efficient processes that minimize waste and maximize productivity.
Another crucial element is the meticulous attention to detail exhibited by Japanese train cleaners. Every step of the cleaning process is carefully planned and executed, ensuring that no area is overlooked. This commitment to thoroughness can be replicated in other industries by adopting a similar approach to cleaning, where every detail is carefully considered.
To apply kaizen principles effectively, organizations should focus on creating a culture of continuous improvement, encouraging employees to identify areas for improvement and suggesting innovative solutions. Leaders should also lead by example, demonstrating their commitment to kaizen and empowering staff to take ownership of their work.
In practical terms, this means establishing regular training sessions, workshops, and feedback mechanisms to ensure that employees are equipped with the necessary skills and knowledge to improve processes and services. Additionally, organizations should recognize and reward employee contributions to innovation and improvement, fostering a sense of accomplishment and motivation among staff.
By embracing kaizen principles, industries can reap significant benefits, including improved cleanliness, increased customer satisfaction, enhanced reputation, and increased productivity. By prioritizing employee engagement, meticulous attention to detail, and continuous improvement, organizations can unlock their full potential and achieve remarkable success.
Achieving Operational Excellence through Efficient Cleaning Processes
Achieving Operational Excellence through Efficient Cleaning Processes
The key to achieving operational excellence lies in the adoption of efficient cleaning processes that prioritize productivity, customer satisfaction, and employee motivation. By streamlining cleaning operations, organizations can unlock significant benefits, including improved cleanliness, increased customer satisfaction, enhanced reputation, and increased productivity.
To achieve operational excellence, it is essential to prioritize employee engagement and empowerment. This can be achieved by investing time and resources into training and motivating cleaning staff, as well as implementing efficient processes that minimize waste and maximize productivity. By fostering a sense of pride and ownership among staff, organizations can unlock increased productivity and efficiency.
Another crucial element in achieving operational excellence is meticulous attention to detail. Every step of the cleaning process should be carefully planned and executed, ensuring that no area is overlooked. This commitment to thoroughness can be replicated in other industries by adopting a similar approach to cleaning, where every detail is carefully considered.
To apply efficient cleaning processes effectively, organizations should focus on creating a culture of continuous improvement, encouraging employees to identify areas for improvement and suggesting innovative solutions. Leaders should also lead by example, demonstrating their commitment to operational excellence and empowering staff to take ownership of their work.
In practical terms, this means establishing regular training sessions, workshops, and feedback mechanisms to ensure that employees are equipped with the necessary skills and knowledge to improve processes and services. Additionally, organizations should recognize and reward employee contributions to innovation and improvement, fostering a sense of accomplishment and motivation among staff.
By embracing efficient cleaning processes, industries can reap significant benefits, including improved cleanliness, increased customer satisfaction, enhanced reputation, and increased productivity. To achieve operational excellence, it is essential to prioritize employee engagement, meticulous attention to detail, and continuous improvement. By doing so, organizations can unlock their full potential and achieve remarkable success.
To get started, consider the following actionable tips:
- Conduct a thorough analysis of your current cleaning processes to identify areas for improvement.
- Invest in training and motivating your cleaning staff to foster a sense of pride and ownership.
- Implement efficient processes that minimize waste and maximize productivity.
- Establish regular feedback mechanisms to encourage employee suggestions and innovations.
- Recognize and reward employee contributions to innovation and improvement.
By following these tips, you can set your organization on the path to achieving operational excellence through efficient cleaning processes.
Recent Posts
- Mastering SEO and Article Writing Techniques Jul 12, 2024
- Exploring Japan's Onsen Culture: A Journey Through Its Top Hot Springs Jul 12, 2024
- A Guide to Hanami: Cherry Blossom Viewing in Japan Jul 12, 2024
- Embracing Minimalism and Wabi-Sabi in Design and Lifestyle Jul 12, 2024
- Exploring Japanese Bento Boxes - A Guide to Tradition, Flavor, and Customization Jul 12, 2024
- Anime Pilgrimage Location Recommendation System Development using Machine Learning Jul 12, 2024
- Exploring Japanese Unagi Eel Cuisine through Sustainable Aquaculture Tech Seminars Jul 12, 2024
- The Power of Mascots in Japan: A Cultural Phenomenon Jul 12, 2024
- Forest Bathing: The Japanese Practice of Shinrin-Yoku Jul 11, 2024
- Unlocking the Fun of Anime-Themed Japanese Suikawari Watermelon Splitting VR Game Development Jul 11, 2024